HPC User Report from M. Fritsche (HS-Coburg)
CFD simulation for the optimization of fans
Professional CFD simulations provide a detailed insight into the flow field within fans. The impact of geometry changes can quickly contribute to optimizing the machine and thus increasing energy efficiency of the fan.
Motivation and problem definition
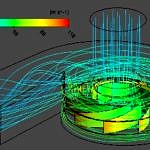
Industrial turbomachines, such as fans and blowers for drying, venting, cooling or conveying tasks, are often used in industrial applications and frequently are a large energy consumer. Thus there is a need for their further optimization and efficiency increase. For large fans and blowers, gaps between moving parts are unavoidable with regard to manufacturing tolerances and possible thermal expansion. In this study, the radial and axial gap between stationary inlet nozzle and rotating impeller and its impact on the performance characteristics are investigated by CFD simulations.
Methods and codes
The turbulent flow field in a turbomachinery is typical three-dimensional, diffusive, dissipative and chaotic. Therefore, the CFD simulations were performed with Reynolds Averaged Navier Stokes equations (RANS) utilizing the commercial code ANSYS CFX. In order to resolve the fluid flow in the gap as well as possible a very fine mesh is required. These simulations are solved in parallel with 24 partitions on the LiMa cluster of the Erlangen Regional Computing Center (RRZE) and afterwards evaluated automatically. This makes it possible to generate more result data in a shorter time compared to conventional desktop computers.
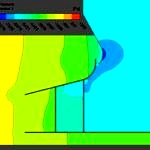
Results
After evaluation of the simulation results it can be stated that the axial and radial gap between the stationary inlet nozzle and the rotating impeller has a significant impact on the expected fan characteristics. The smaller the gaps the lower the leakage flow rate and correspondingly the better the achievable characteristics. Due to the powerful computer resources of the LiMa cluster a variety of geometry variations could be performed to obtain an optimal design of the inlet nozzle.
Outreach
The detailed results are currently being prepared for an ASME journal publication.
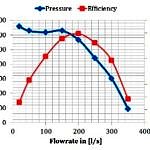
Researcher’s Bio and Affiliation
Manuel Fritsche received his master degree in development and management in mechanical engineering and automotive at Coburg University. He is currently working there as a research assistant in the team of Prof. Dr.-Ing. Philipp Epple in the field of fan’s optimization and he is also PhD student of Prof. Dr.-Ing. habil. Antonio Delgado at the Institute of Fluid Mechanics (LSTM) at the Friedrich-Alexander-Universität Erlangen-Nürnberg.