HPC User Report from J. Köpf (Chair of Materials Science and Engineering for Metals)
3D study: Impact of parameters on additively build components
The impact of various build parameters on the resulting grain structure of additively built components is investigated numerically. The results enable the tailoring of the microstructure and thus the component properties for individual applications.
Motivation and problem definition
Beam-based additive manufacturing offers huge potential, but also great challenges. One of these challenges is the prediction of the resulting grain structure of the asbuilt part. The grain structure is of special interest because of its enormous influence on the resulting component properties. Fine tuning grain structure in the manufactured part requires a detailed understanding of the influence of build parameters like power and velocity of the beam as well as different hatching strategies. Numerical simulations enable the prediction of the microstructure resulting from specific beam parameters, dispensing with the need for tedious calibration experiments. The underlying algorithms are extremely computational intensive, resulting in computation times of several months on a single workstation. Utilization of massively parallel processing on a high-performance cluster computer allows the computation of the grain structure of a part consisting of a huge number of layers within several days.
Methods and codes
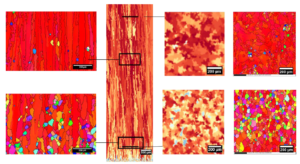
The simulations are conducted with the MPI parallelized in-house software SAMPLE3D_GS written in C++. It is based on a cellular automaton grain structure algorithm originally introduced by Gandin and Rappaz. The heat input is calculated using an analytical solution of the transient heat conduction equation.
Results
Figure 1 shows the comparison of a simulated grain structure (center) with EBSD measurements (borders). Both longitudinal (left side) as well as traversal (right side) cross section cuts are in excellent agreement.
Outreach
The project part of the SFB 814 funded by the DFG.
Results of this work have been shown on the following conferences:
- International Conference on Additive Technologies: iCAT (2016)
- 1st ECCOMAS Thematic Conference on Simulation for Additive Manufacturing SimAM (2017)
- 5. Industriekolloquium des Sonderforschungsbereichs 814 – Additive Fertigung (2017)
A couple of journal contributions on this work are in progress.
Researcher’s Bio and Affiliation
Johannes Köpf studied material science at the Friedrich-Alexander-Universität Erlangen-Nürnberg (FAU) and graduated in 2004. He worked as a project engineer at Neue Materialien Fürth Gmbh (NMF) until 2011 and as research associate at Zentralinstitut für Neue Materialien und Prozesstechnik (ZMP) until 2013. In 2014 he started as a PhD student at the Chair of Materials Science and Engineering for Metals (FAU) under the supervision of Dr.-Ing. Matthias Markl and Prof. Dr.-Ing. habil. Carolin Körner.